New Study Shows 3D-Printed Splints Are a Safe and Effective Alternative for Treating Distal Radius Fractures
A recent study, employing the Spentys software for the creation of custom 3D-printed splints, marks a significant addition to the literature in the outcomes of treatment of distal radial fractures. The study aimed to assess whether these 3D printed splints were just as good - if not better - than the traditional alternatives.
This research also corroborates the safety and effectiveness of these innovative orthoses, presenting them as a compelling alternative to conventional fiberglass casts. With particular benefits for younger and more active patients.
A Comparative Study: 3D Printed Splints Vs. Fiberglass Casts
The study involved 39 patients suffering from minimally displaced distal radial fractures. These patients were divided randomly into two groups. One group received traditional immobilization with a fiberglass cast, while the other group was fitted with a 3D-printed splint for the forearm. Each splint, featuring a three-quarter circumferential design with a dorsoulnar longitudinal opening and fixation loops, was custom-made using certified Spentys software and then converted into a stereolithography (STL) file.
These 3D-printed splints were created by first using a handheld device to scan the patient's forearm surface, thus gathering the necessary digital data. This data was then used in-house to fabricate the splints via digital light processing printing technology.
The primary objective of this study was to compare the efficacy and patient satisfaction of these 3D-printed splints to that of conventional fiberglass casts in a point-of-care (POC) setting.
The Results: Patient Satisfaction and Clinical Effectiveness
Patient satisfaction and clinical effectiveness were measured at 1 and 6 weeks after the beginning of immobilization. Fracture healing, pain, range of motion, grip strength, and the DASH and PRWE scores were assessed up to a 1-year follow-up.
The results of the study showed that the 3D-printed splints were equally well tolerated by the patients and were just as clinically effective as the conventional fiberglass casts. However, there was a higher rate of minor complications associated with the 3D printed splints.
Interestingly, the study found that younger, tech-savvy patients under the age of 50 preferred the 3D printed splints. They appreciated the lighter weight, water resistance, and modern aesthetics of the 3D-printed models. However, older patients, especially women, had more issues with the rigidity of the printed splints.
Spentys and the Future of 3D Printed Orthoses
Spentys, a leading software used in this study for producing 3D printed splints, is proud to be at the forefront of this innovative technology. As this study shows, 3D printed splints present a safe and equally effective alternative to conventional casts, especially for young and active patients.
The Spentys workflow played an integral part in the study and proved to be an intuitive way to quickly design hand splints. To learn more about our workflow, request a demo with us here.
We believe that 3D printing technology is evolving and that continuous research and development are necessary to optimize the workflow and production process. It was an honor to collaborate with the Department of Orthopaedic Surgery and Traumatology, Hand and Peripheral Nerve Surgery, Kantonsspital Baselland, and the Department of Biomedical Engineering, Medical Additive Manufacturing Research Group (MAM), University of Basel, for this study.
To read more details on the study, please visit https://pubmed.ncbi.nlm.nih.gov/37458129/

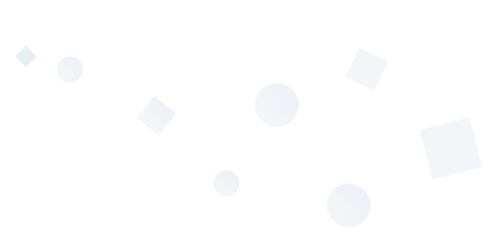
New Study Shows 3D-Printed Splints Are a Safe and Effective Alternative for Treating Distal Radius Fractures

A recent study, employing the Spentys software for the creation of custom 3D-printed splints, marks a significant addition to the literature in the outcomes of treatment of distal radial fractures. The study aimed to assess whether these 3D printed splints were just as good - if not better - than the traditional alternatives.
This research also corroborates the safety and effectiveness of these innovative orthoses, presenting them as a compelling alternative to conventional fiberglass casts. With particular benefits for younger and more active patients.
A Comparative Study: 3D Printed Splints Vs. Fiberglass Casts
The study involved 39 patients suffering from minimally displaced distal radial fractures. These patients were divided randomly into two groups. One group received traditional immobilization with a fiberglass cast, while the other group was fitted with a 3D-printed splint for the forearm. Each splint, featuring a three-quarter circumferential design with a dorsoulnar longitudinal opening and fixation loops, was custom-made using certified Spentys software and then converted into a stereolithography (STL) file.
These 3D-printed splints were created by first using a handheld device to scan the patient's forearm surface, thus gathering the necessary digital data. This data was then used in-house to fabricate the splints via digital light processing printing technology.
The primary objective of this study was to compare the efficacy and patient satisfaction of these 3D-printed splints to that of conventional fiberglass casts in a point-of-care (POC) setting.
The Results: Patient Satisfaction and Clinical Effectiveness
Patient satisfaction and clinical effectiveness were measured at 1 and 6 weeks after the beginning of immobilization. Fracture healing, pain, range of motion, grip strength, and the DASH and PRWE scores were assessed up to a 1-year follow-up.
The results of the study showed that the 3D-printed splints were equally well tolerated by the patients and were just as clinically effective as the conventional fiberglass casts. However, there was a higher rate of minor complications associated with the 3D printed splints.
Interestingly, the study found that younger, tech-savvy patients under the age of 50 preferred the 3D printed splints. They appreciated the lighter weight, water resistance, and modern aesthetics of the 3D-printed models. However, older patients, especially women, had more issues with the rigidity of the printed splints.
Spentys and the Future of 3D Printed Orthoses
Spentys, a leading software used in this study for producing 3D printed splints, is proud to be at the forefront of this innovative technology. As this study shows, 3D printed splints present a safe and equally effective alternative to conventional casts, especially for young and active patients.
The Spentys workflow played an integral part in the study and proved to be an intuitive way to quickly design hand splints. To learn more about our workflow, request a demo with us here.
We believe that 3D printing technology is evolving and that continuous research and development are necessary to optimize the workflow and production process. It was an honor to collaborate with the Department of Orthopaedic Surgery and Traumatology, Hand and Peripheral Nerve Surgery, Kantonsspital Baselland, and the Department of Biomedical Engineering, Medical Additive Manufacturing Research Group (MAM), University of Basel, for this study.
To read more details on the study, please visit https://pubmed.ncbi.nlm.nih.gov/37458129/
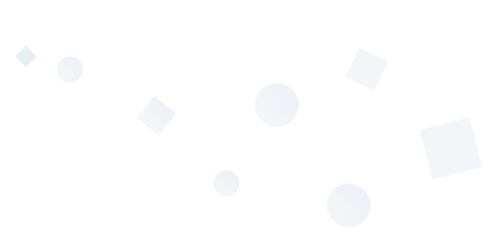
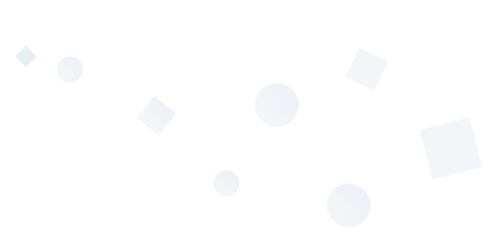