3D technology building the future of orthopedics at Kantonsspital Baselland
If a single element is fundamental to the development and future of orthopedics, it’s research.
To be precise, high-quality clinical research that evaluates the current and potential practices, methods, and technologies is key to delivering evidence-based orthopedic devices.
That became clear to us early on, which is why we decided to make research an intrinsic part of what we do at Spentys.
Research is essential to us for these two reasons:
1. Research helps deliver better orthoses.
The more we understand the needs of patients and their feedback, the better orthoses we can create. Research also helps the professionals better predict the outcome of their therapy, care, or surgery.
2. Research helps us test and improve the entire Spentys system.
Research helps us validate how the Spentys solution works for practitioners and helps us understand how to make it even better. We are constantly improving and updating our system.
That is why we collaborate with those using our system, such as Kantonsspital Baselland.
Kantonsspital Baselland: a clinical trial for 3D-printed forearm orthoses
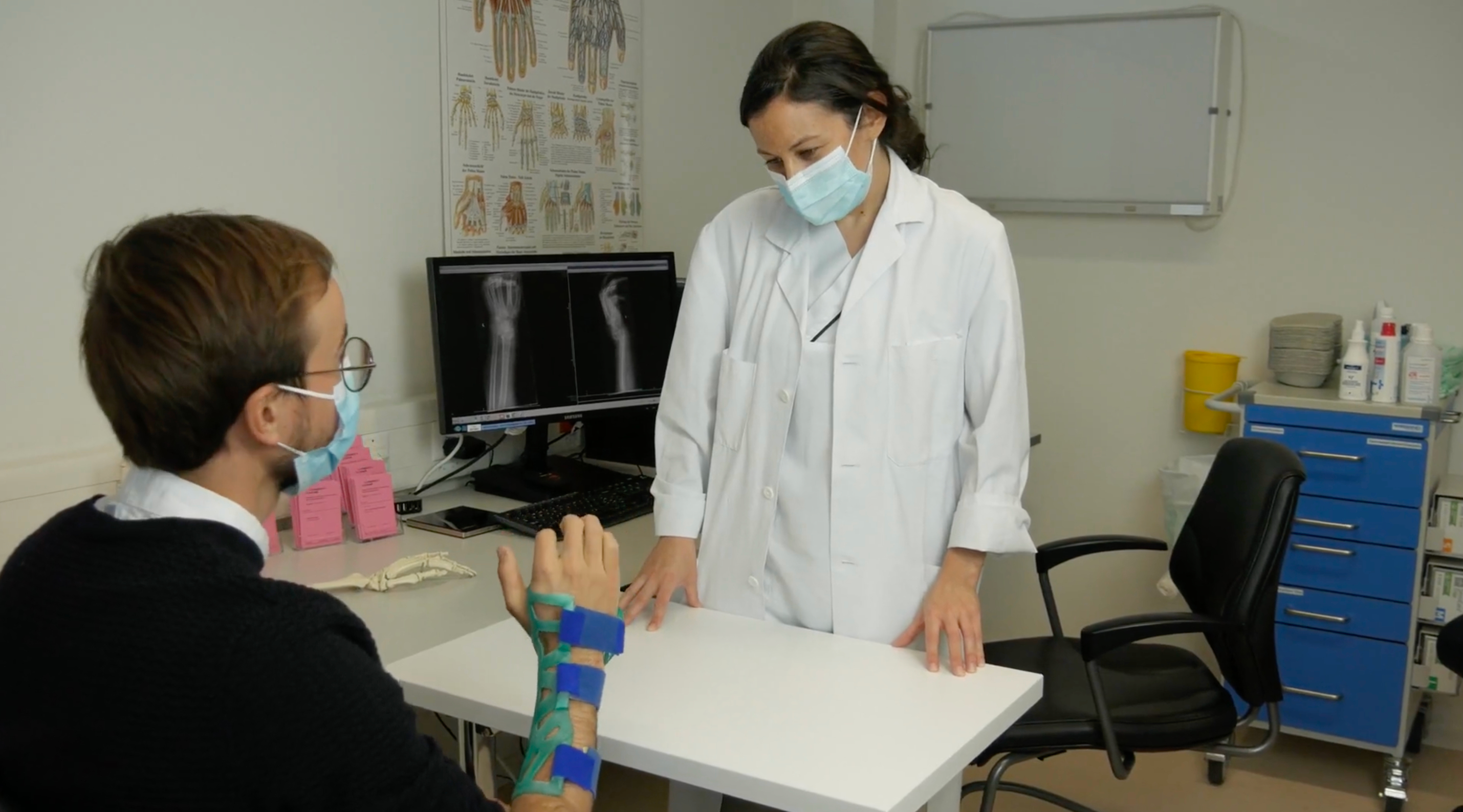
Background:
Kantonsspital Baselland is a hospital in Switzerland that was already using 3D technology for training young surgeons and patient communication. They decided to set up a randomized clinical trial assessing and comparing 3D-printed forearm casts to conventionally made ones. To our knowledge, this is the first study of this kind.
Generally speaking, there is not much clinical research around 3D technology largely due to the lack of purpose-built scanning applications, complicated digital design software, and lengthy error-prone printing processes.
We decided to support this study with the Spentys solution.
What we did:
Spentys proposed a multidisciplinary workflow for in-hospital mass production of patient-specific 3D-printed devices for hand and wrist rehabilitation. We helped the team implement our workflow and gave training to get them started.
We also supported the hospital in testing. We set up a randomized controlled trial to analyze the relevance, feasibility, safety, and patient comfort of 3D-printed forearm orthoses. Further, we compared these with the traditional methods, such as plaster casts.
We also collected patient feedback during the study using two surveys specially made for this purpose.
Challenges:
Kantonsspital Baselland's team was interested in analysing and comparing 3D-printed orthoses mainly because the conventional hand and wrist orthoses pose certain challenges.
We can group the challenges into these three main categories:
1. Fitting
The fitting greatly depends on the clinician's skill and experience because of their reversibility of these materials and body-based contact models. In traditional processes, poor fitting may cause more pain or lead to inadequate immobilization.
2. Weight
Conventional orthoses are bulky, heavy, poorly ventilated and unsightly, causing an obvious inconvenience in the daily lives of the patients. For these reasons, patients regularly report low satisfaction levels during rehabilitation.
3. Hygiene
In addition to all the above, keeping orthoses clean and dry is difficult. Different studies have show that this also increases the risk of infection.
Outcomes:
First, it is important to mention that because we implemented a digital workflow into the hospital's practice, the entire process of making orthoses is simplified. The digital workflow consists of roughly three steps: scanning, printing, and post-processing.
Yet, more importantly, the first patients’ feedback shows good acceptance and satisfaction. Even though these were relatively low-cost orthoses(approximately 6 USD per cast), patients reported comfort and were generally enthusiastic with the experience.
The study demonstrated that 3D-printed orthoses are a valuable substitute for traditional treatment methods and represent added value for the patient and the medical world.
We summarised the patient feedback in this video:
We are currently looking for new partners who wish to run clinical trials and studies.
Whether you want to explore possibilities, do a trial project, or want to start using 3D printing for all your patients, Spentys can help you set up everything in the best way possible.
Want to explore the possibilities?
Get in touch here.
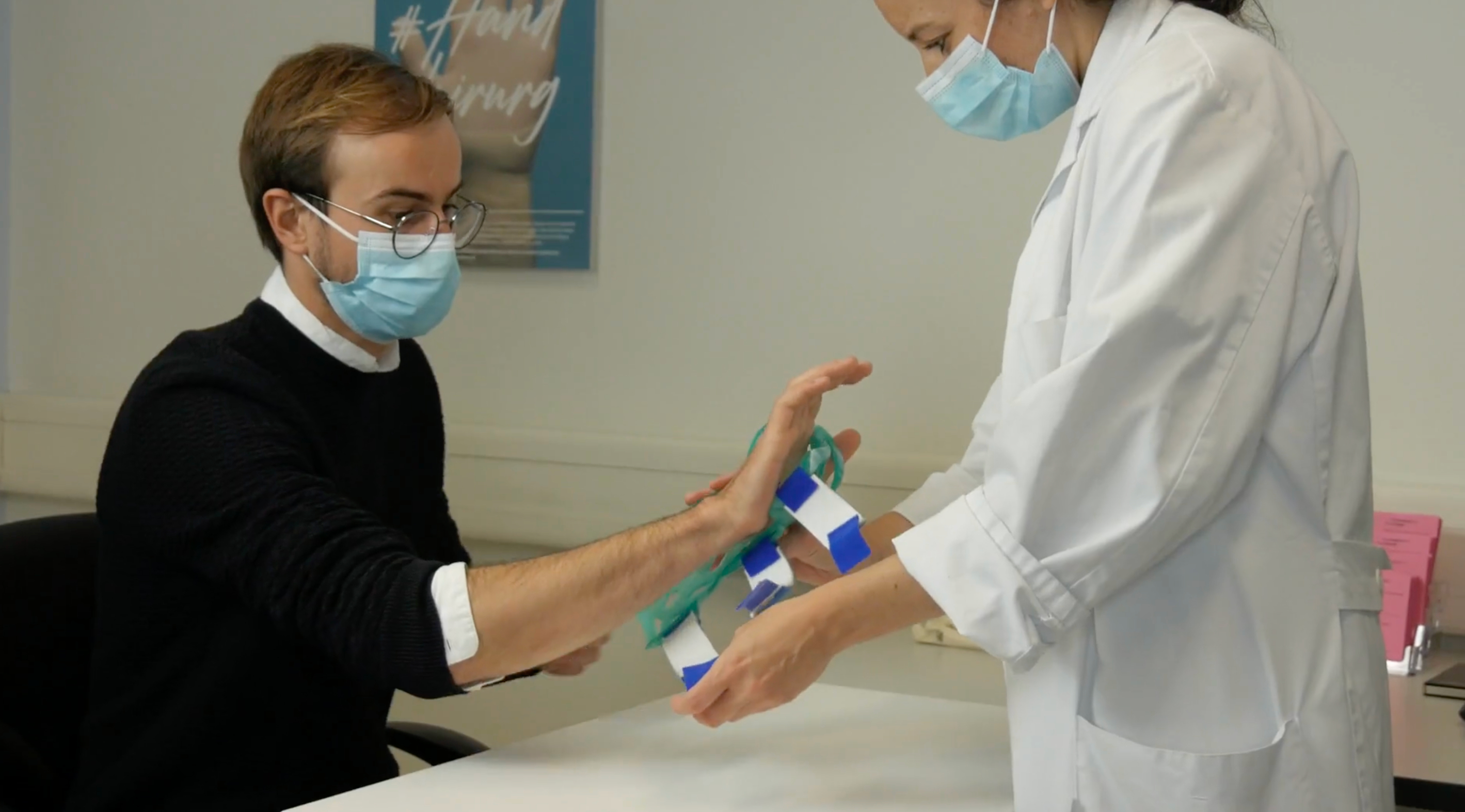
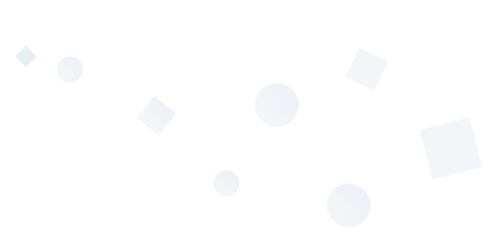
3D technology building the future of orthopedics at Kantonsspital Baselland
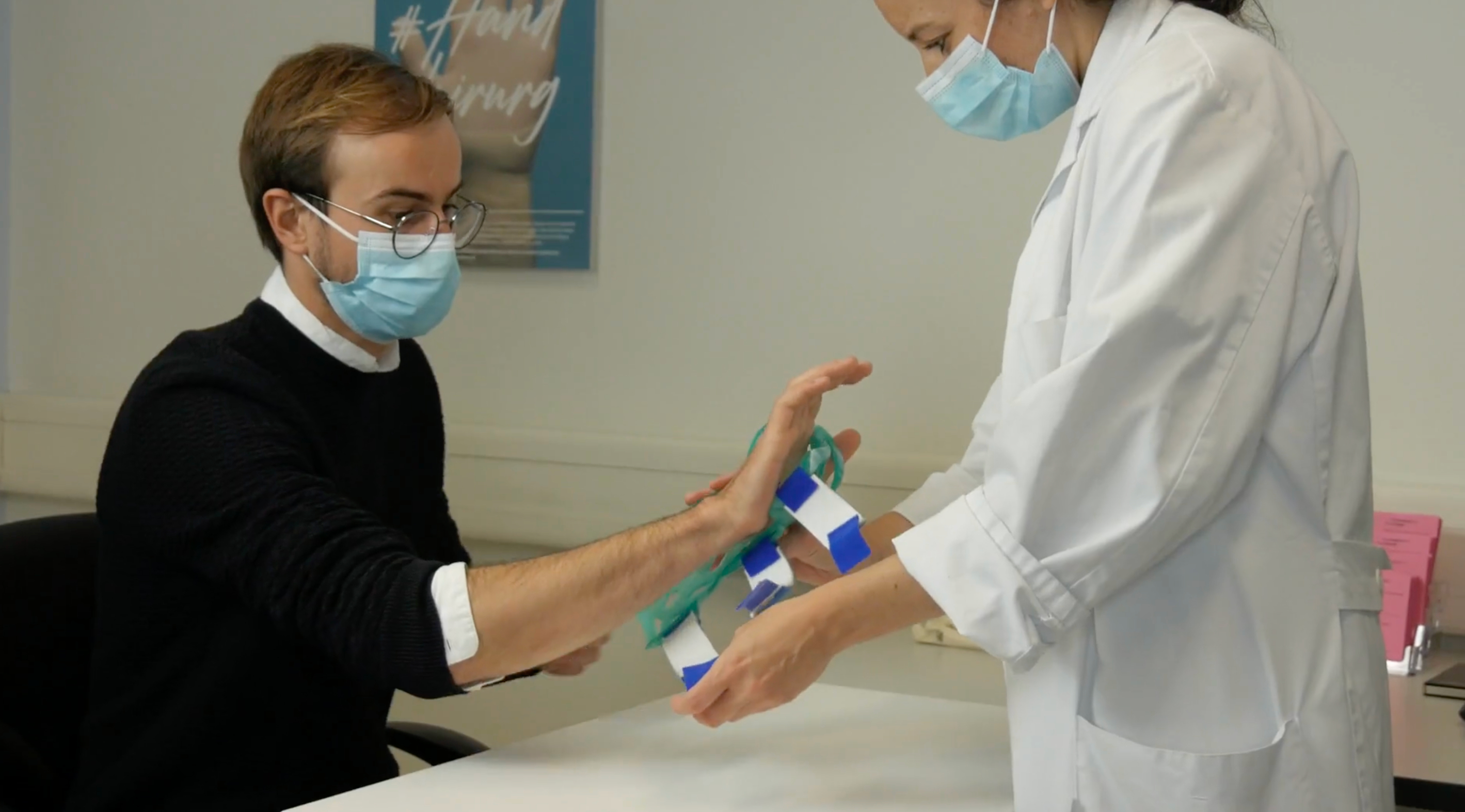
If a single element is fundamental to the development and future of orthopedics, it’s research.
To be precise, high-quality clinical research that evaluates the current and potential practices, methods, and technologies is key to delivering evidence-based orthopedic devices.
That became clear to us early on, which is why we decided to make research an intrinsic part of what we do at Spentys.
Research is essential to us for these two reasons:
1. Research helps deliver better orthoses.
The more we understand the needs of patients and their feedback, the better orthoses we can create. Research also helps the professionals better predict the outcome of their therapy, care, or surgery.
2. Research helps us test and improve the entire Spentys system.
Research helps us validate how the Spentys solution works for practitioners and helps us understand how to make it even better. We are constantly improving and updating our system.
That is why we collaborate with those using our system, such as Kantonsspital Baselland.
Kantonsspital Baselland: a clinical trial for 3D-printed forearm orthoses
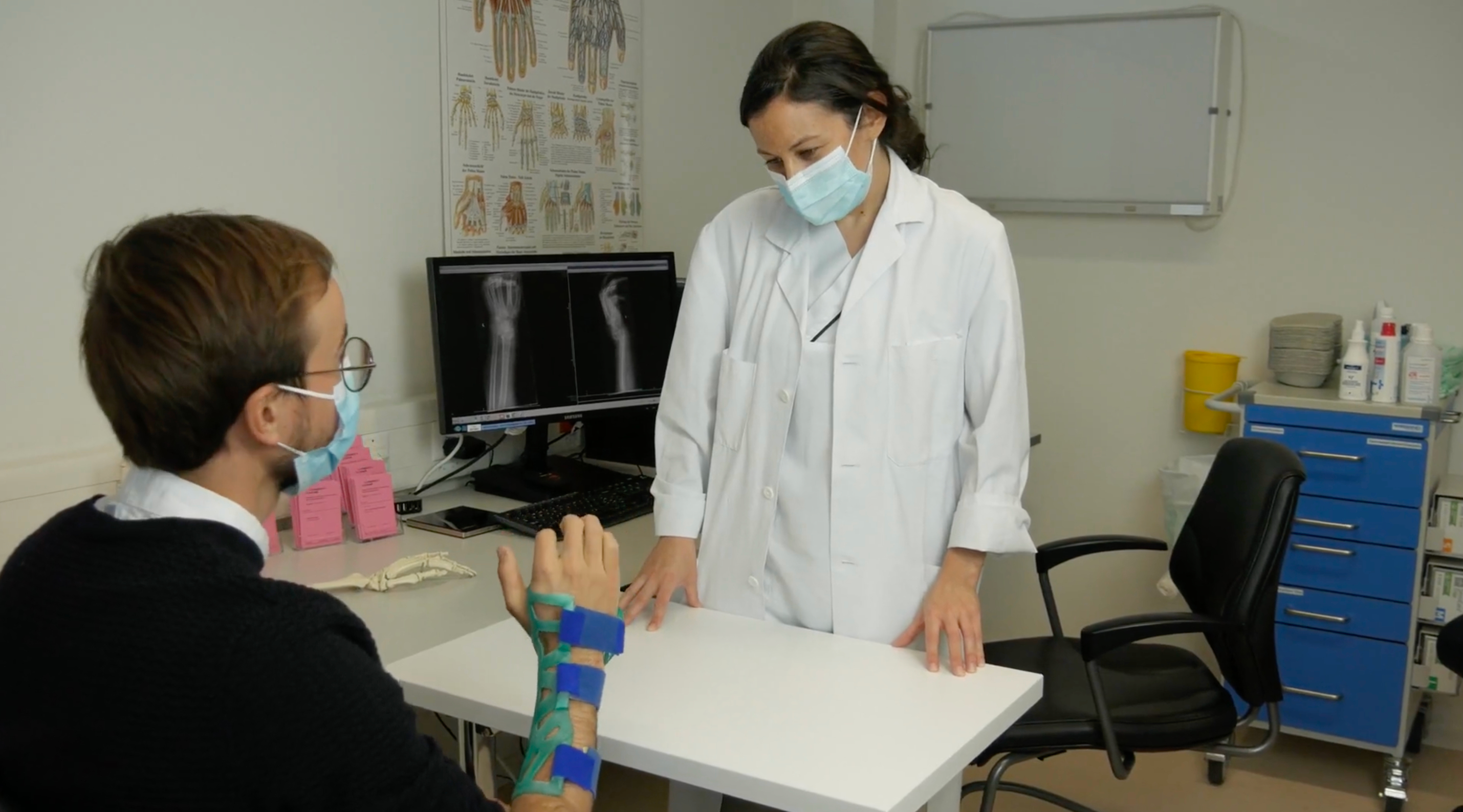
Background:
Kantonsspital Baselland is a hospital in Switzerland that was already using 3D technology for training young surgeons and patient communication. They decided to set up a randomized clinical trial assessing and comparing 3D-printed forearm casts to conventionally made ones. To our knowledge, this is the first study of this kind.
Generally speaking, there is not much clinical research around 3D technology largely due to the lack of purpose-built scanning applications, complicated digital design software, and lengthy error-prone printing processes.
We decided to support this study with the Spentys solution.
What we did:
Spentys proposed a multidisciplinary workflow for in-hospital mass production of patient-specific 3D-printed devices for hand and wrist rehabilitation. We helped the team implement our workflow and gave training to get them started.
We also supported the hospital in testing. We set up a randomized controlled trial to analyze the relevance, feasibility, safety, and patient comfort of 3D-printed forearm orthoses. Further, we compared these with the traditional methods, such as plaster casts.
We also collected patient feedback during the study using two surveys specially made for this purpose.
Challenges:
Kantonsspital Baselland's team was interested in analysing and comparing 3D-printed orthoses mainly because the conventional hand and wrist orthoses pose certain challenges.
We can group the challenges into these three main categories:
1. Fitting
The fitting greatly depends on the clinician's skill and experience because of their reversibility of these materials and body-based contact models. In traditional processes, poor fitting may cause more pain or lead to inadequate immobilization.
2. Weight
Conventional orthoses are bulky, heavy, poorly ventilated and unsightly, causing an obvious inconvenience in the daily lives of the patients. For these reasons, patients regularly report low satisfaction levels during rehabilitation.
3. Hygiene
In addition to all the above, keeping orthoses clean and dry is difficult. Different studies have show that this also increases the risk of infection.
Outcomes:
First, it is important to mention that because we implemented a digital workflow into the hospital's practice, the entire process of making orthoses is simplified. The digital workflow consists of roughly three steps: scanning, printing, and post-processing.
Yet, more importantly, the first patients’ feedback shows good acceptance and satisfaction. Even though these were relatively low-cost orthoses(approximately 6 USD per cast), patients reported comfort and were generally enthusiastic with the experience.
The study demonstrated that 3D-printed orthoses are a valuable substitute for traditional treatment methods and represent added value for the patient and the medical world.
We summarised the patient feedback in this video:
We are currently looking for new partners who wish to run clinical trials and studies.
Whether you want to explore possibilities, do a trial project, or want to start using 3D printing for all your patients, Spentys can help you set up everything in the best way possible.
Want to explore the possibilities?
Get in touch here.
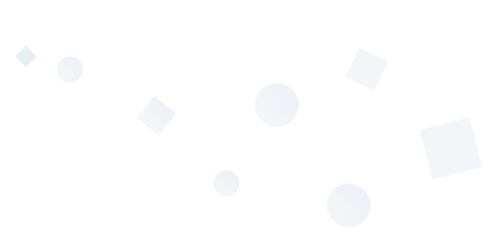
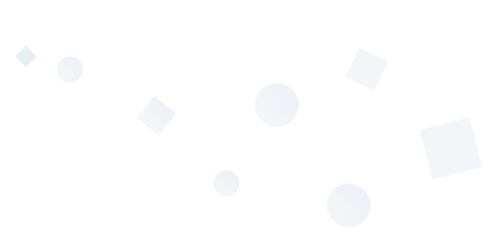