How Ortho-Lotz is using 3D technologies for the manufacturing of custom-made orthopaedic shoes.
Orthopaedic shoes are complex medical devices intended for patients with foot deformities due to amputation or pathologies such as diabetes or paraplegia. Their purpose is to place the foot in a stable position, correct joint problems, relieve pain, and make walking more comfortable again. Custom-made orthopaedic shoes are needed in cases where simple modifications to standard orthopaedic shoes and plantar supports are not sufficient. Creating these medical devices demands true craftsmanship and a lot of experience. Ortho-Lotz was able to add 3D technology to their set of tools, and thereby remove tedious bottlenecks from the manufacturing process.
“The Spentys platform allows our pedorthists to manufacture custom orthopaedic shoes of higher quality and with more precision. Furthermore, the overall production time can be decreased with 3D printing techniques; hence the patients get their new pair faster.” ~ Emilien Bossert, Pedorthist at Ortho-Lotz
The traditional manufacturing of custom-made orthopaedic shoes is a long endeavour that requires the input of several craftsmen. In general, it takes 1 to 2 months before the orthopaedic shoes can be delivered to the patient. Here are the main steps of the traditional manufacturing process:
‍
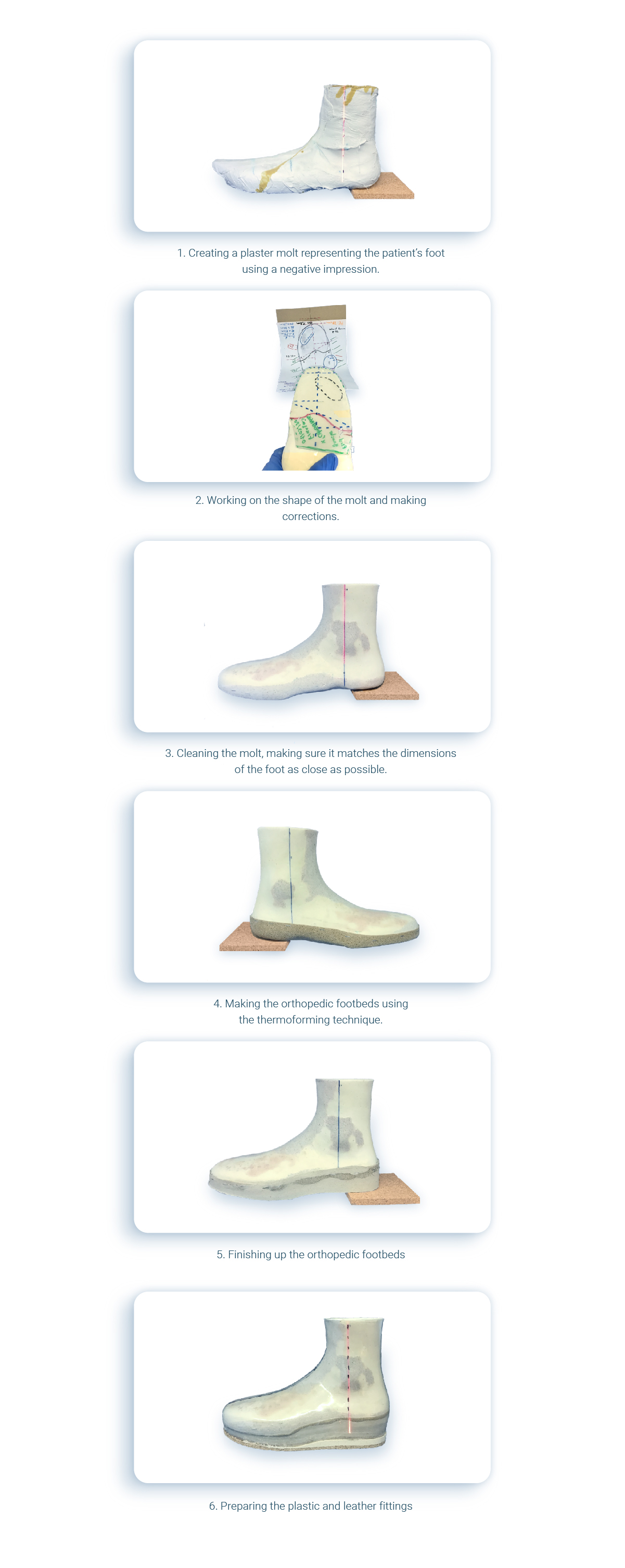
The traditional process of making a custom-made orthopaedic shoe is one with many challenges. Some parts of the process can be improved with the introduction of new technologies. Let’s have a look at two of these challenges:
- After casting the mould, we obtain a positive model in the shape of the foot without the front-end part (because of the limitations of the plaster cast). Hence, a formwork must be created of the front-end of the foot to pour a non-extensible resin into the formwork completing the shape of the whole shoe. This step requires at least two hours of manual work; making the mould, putting the tapes on, and pouring the resin. After which, the resin has to dry for a couple of hours.
- For patients with amputees, in particular, a prosthetic foot is created (similar to the other foot) to fill the patient's shoe. The challenge here lies in the material used for the prosthetic foot. It is often made from soft material, making it almost impossible to create a model on it. Consequentially, the material deforms, and the aesthetics of the original shoe are lost. Traditionally, the pedorthist must fabricate a rigid copy of the soft prosthetic. That’s why the pedorthist prepares plastic fittings that have exactly the volume and shape of the prosthetic foot in order to permanently compare the copy to the original shape. This procedure takes half a day of work on average.
It is possible to accelerate the manufacturing process. Together with the Ortho-Lotz team, we implemented 3D technologies to save time while creating orthopaedic shoes that fit better to the feet. Here is how we were able to streamline the process.
First, Instead of making a formwork at the front-end of the foot, using 3D printers, we created toecaps. These plastic caps are being placed on the feet before casting the toes of the patient's feet. The result is a complete shape rather than one that doesn’t include the toes. The toe caps are directly integrated into the mould, and there is no need to make the formwork. Several shapes and sizes have been printed. The material used for the toe caps is TPU, a soft and flexible material that can be slightly deformed to fit the foot as closely as possible.
Furthermore, the rigid copy of the prosthetic foot can be 3D printed. Using a 3D scanner with a sufficient resolution (0,05 mm), we are able to get a digital copy of the prosthetic foot, which can be printed out with your machine of choice. Here are some technical specifications to keep in mind:
- The filling must be optimal in order to allow staples to be planted in it (we used a 30% filling with a wall thickness of 7mm).
- Cuts must be made in the 3D model in order to be able to remove the mould from the shoe once the work is completed.
Over time, the usage of 3D technologies at Ortho-Lotz has increased and diversified. Today, the pedorthists at Ortho-Lotz use the copies of the foot shape to make pairs of low-top shoes from pairs of high-top shoes or vice versa. For this, a scan of the low-top last is made, and the model is modified to fit the high-top last.
Conclusion:
3D technologies have allowed the Ortho-Lotz team to save time, gain in precision, and consequently accelerate and improve workshop operations for pedorthists. Our technology can be used as an extra tool to complete, substitute, or enhance traditional methods to make processes simpler, faster, and more accurate. Our goal here at Spentys is to facilitate the usage of 3D technologies for a frictionless integration with your craftmanship.
‍
.jpeg)
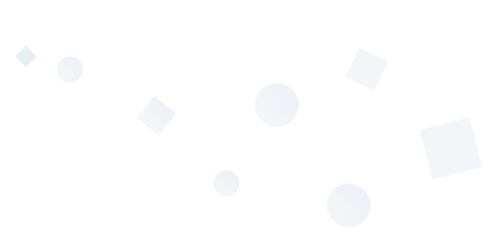
How Ortho-Lotz is using 3D technologies for the manufacturing of custom-made orthopaedic shoes.
.jpeg)
Orthopaedic shoes are complex medical devices intended for patients with foot deformities due to amputation or pathologies such as diabetes or paraplegia. Their purpose is to place the foot in a stable position, correct joint problems, relieve pain, and make walking more comfortable again. Custom-made orthopaedic shoes are needed in cases where simple modifications to standard orthopaedic shoes and plantar supports are not sufficient. Creating these medical devices demands true craftsmanship and a lot of experience. Ortho-Lotz was able to add 3D technology to their set of tools, and thereby remove tedious bottlenecks from the manufacturing process.
“The Spentys platform allows our pedorthists to manufacture custom orthopaedic shoes of higher quality and with more precision. Furthermore, the overall production time can be decreased with 3D printing techniques; hence the patients get their new pair faster.” ~ Emilien Bossert, Pedorthist at Ortho-Lotz
The traditional manufacturing of custom-made orthopaedic shoes is a long endeavour that requires the input of several craftsmen. In general, it takes 1 to 2 months before the orthopaedic shoes can be delivered to the patient. Here are the main steps of the traditional manufacturing process:
‍
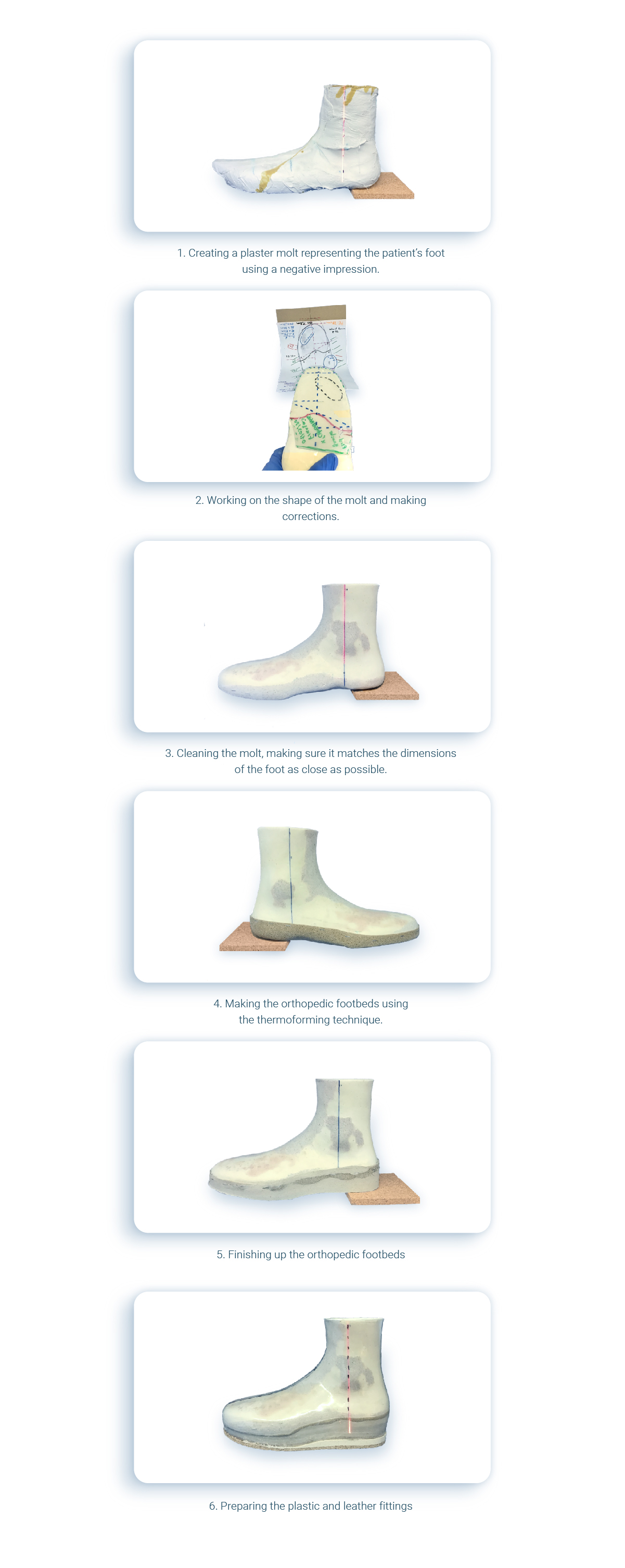
The traditional process of making a custom-made orthopaedic shoe is one with many challenges. Some parts of the process can be improved with the introduction of new technologies. Let’s have a look at two of these challenges:
- After casting the mould, we obtain a positive model in the shape of the foot without the front-end part (because of the limitations of the plaster cast). Hence, a formwork must be created of the front-end of the foot to pour a non-extensible resin into the formwork completing the shape of the whole shoe. This step requires at least two hours of manual work; making the mould, putting the tapes on, and pouring the resin. After which, the resin has to dry for a couple of hours.
- For patients with amputees, in particular, a prosthetic foot is created (similar to the other foot) to fill the patient's shoe. The challenge here lies in the material used for the prosthetic foot. It is often made from soft material, making it almost impossible to create a model on it. Consequentially, the material deforms, and the aesthetics of the original shoe are lost. Traditionally, the pedorthist must fabricate a rigid copy of the soft prosthetic. That’s why the pedorthist prepares plastic fittings that have exactly the volume and shape of the prosthetic foot in order to permanently compare the copy to the original shape. This procedure takes half a day of work on average.
It is possible to accelerate the manufacturing process. Together with the Ortho-Lotz team, we implemented 3D technologies to save time while creating orthopaedic shoes that fit better to the feet. Here is how we were able to streamline the process.
First, Instead of making a formwork at the front-end of the foot, using 3D printers, we created toecaps. These plastic caps are being placed on the feet before casting the toes of the patient's feet. The result is a complete shape rather than one that doesn’t include the toes. The toe caps are directly integrated into the mould, and there is no need to make the formwork. Several shapes and sizes have been printed. The material used for the toe caps is TPU, a soft and flexible material that can be slightly deformed to fit the foot as closely as possible.
Furthermore, the rigid copy of the prosthetic foot can be 3D printed. Using a 3D scanner with a sufficient resolution (0,05 mm), we are able to get a digital copy of the prosthetic foot, which can be printed out with your machine of choice. Here are some technical specifications to keep in mind:
- The filling must be optimal in order to allow staples to be planted in it (we used a 30% filling with a wall thickness of 7mm).
- Cuts must be made in the 3D model in order to be able to remove the mould from the shoe once the work is completed.
Over time, the usage of 3D technologies at Ortho-Lotz has increased and diversified. Today, the pedorthists at Ortho-Lotz use the copies of the foot shape to make pairs of low-top shoes from pairs of high-top shoes or vice versa. For this, a scan of the low-top last is made, and the model is modified to fit the high-top last.
Conclusion:
3D technologies have allowed the Ortho-Lotz team to save time, gain in precision, and consequently accelerate and improve workshop operations for pedorthists. Our technology can be used as an extra tool to complete, substitute, or enhance traditional methods to make processes simpler, faster, and more accurate. Our goal here at Spentys is to facilitate the usage of 3D technologies for a frictionless integration with your craftmanship.
‍
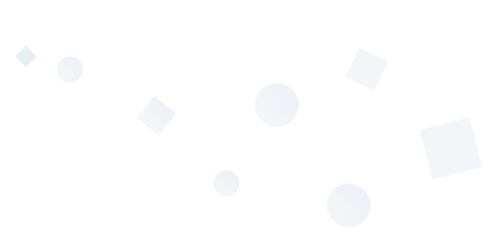
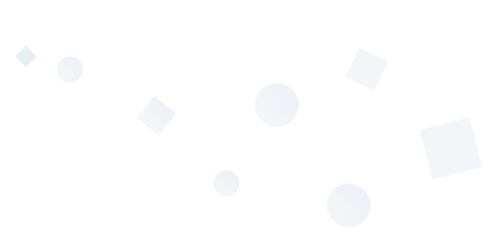